2025-02-15
Komponenten von Roboterschweißsystemen: Ein umfassender Überblick
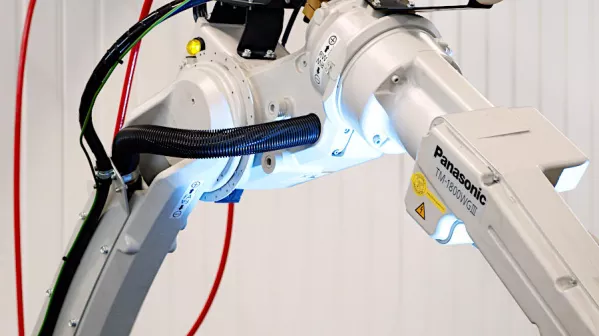
Roboterschweißen ist heute ein zentrales Element moderner Fertigungsprozesse in vielen Industriezweigen. Die dynamische Entwicklung dieser Technologie trägt maßgeblich zur Steigerung von Produktivität, Qualität und Sicherheit der Schweißprozesse bei. Die Grundlage eines effizienten Roboterschweißsystems bildet die richtige Konfiguration seiner Komponenten, die gemeinsam eine integrierte, präzise und zuverlässige Fertigungsstation bilden. Dieser Artikel bietet eine detaillierte Analyse der Hauptkomponenten von Roboterschweißsystemen, ihre technischen Besonderheiten und funktionalen Zusammenhänge.
1. Roboterarm und seine Eigenschaften
1.1. Roboterarten im Schweißen
In Schweißanwendungen werden vorwiegend serielle (anthropomorphe) Roboter eingesetzt, die sich durch hohe Vielseitigkeit und Flexibilität auszeichnen. Am weitesten verbreitet sind 6-Achs-Konfigurationen, die eine Positionierung des Schweißwerkzeugs in jedem beliebigen Winkel im Arbeitsraum ermöglichen. In speziellen Anwendungen kommen auch folgende Roboter zum Einsatz:
- SCARA-Roboter – hauptsächlich für das Schweißen flacher Bauteile
- Parallelkinematik-Roboter – für Anwendungen mit hoher Dynamik
- Portalroboter (Gantry-Systeme) – für das Schweißen großformatiger Konstruktionen
1.2. Technische Parameter von Schweißrobotern
Zu den wichtigsten Parametern von Schweißrobotern gehören:
- Traglast – typischerweise 6–210 kg (einschließlich Schweißbrenner)
- Arbeitsbereich – von 1,4 m für kleine Anwendungen bis über 3,5 m für Großroboter
- Wiederholgenauigkeit – ±0,05–0,1 mm
- Freiheitsgrade – meist 6 Achsen, in anspruchsvollen Anwendungen auch 7-Achs-Lösungen
- Bewegungsgeschwindigkeit – bis zu 2 m/s für schnelles Positionieren zwischen Schweißpunkten
- Umgebungsbeständigkeit – spezielle Schutzhüllen gegen Schweißspritzer und Staub
1.3. Spezialisierte Konstruktionslösungen
In Schweißrobotern kommen verschiedene spezialisierte Lösungen zum Einsatz:
- Innenverlegte Kabel (Hollow Wrist) – für Strom- und Steuerleitungen
- Schutzbeschichtungen – resistent gegen Schweißspritzer
- Kühlsysteme für Gelenke – bei hoher thermischer Belastung
- Verstärkte Roboterhandgelenke – für stabile Schweißprozessführung
2. Schweißwerkzeuge
2.1. Schweißbrenner
Brenner sind das zentrale Verbindungselement zwischen Roboter und Schweißprozess. Folgende Typen werden unterschieden:
2.1.1. MIG/MAG-Brenner
- Luftgekühlt (bis 250–300 A)
- Flüssigkeitsgekühlt (bis 500–600 A)
- Mit automatischer Reinigung (TCP – Tool Center Point)
- Mit integrierten Sensoren (Lichtbogenspannung, Temperatur, Gasfluss)
2.1.2. WIG-Brenner
- Standard-Wolframelektrodenbrenner
- Mit Kaltdrahtzufuhr
- Mit Schnellwechselsystem für Elektroden
- Spezialbrenner für hohe Stromstärken
2.1.3. Laserschweißköpfe
- Optische Systeme zur Strahlformung
- Hybride Schweißköpfe (Laser + MIG/MAG)
- Scansysteme für Schweißen ohne Roboterbewegung
2.2. Drahtvorschubsysteme
Präzise und zuverlässige Drahtzufuhr ist entscheidend für den Roboterschweißprozess:
2.2.1. Drahtvorschubgeräte
- Push-Systeme – Antrieb naht der Drahtspule
- Pull-Systeme – Antrieb naht dem Brenner
- Push-Pull-Systeme – beste Kontrolle über lange Distanzen
- Servoantriebe – präzise Regelung der Vorschubgeschwindigkeit
2.2.2. Drahtspulen und -trommeln
- Standardschweißdrahtspulen (5–18 kg)
- Großtrommeln (100–300 kg) für Serienfertigung
- Schnellwechselsysteme zur Minimierung von Stillstandszeiten
2.2.3. Drahtführungen
- Flexible Schläuche für verschiedene Materialien (Aluminium, Stahl, Sonderlegierungen)
- Rollenführungen für weiche Materialien
- Spezialführungen mit geringer Reibung für Fülldraht
2.3. Halterungen und Brennerbefestigungen
Die Befestigung des Brenners am Roboter beeinflusst die Prozessgenauigkeit:
- Starre Halterungen für Standardanwendungen
- Nachgiebige Befestigungen zur Kompensation von Positionierungsungenauigkeiten
- Schnellwechselsysteme (QCS – Quick Change System)
- Kollisionsgeschützte Halterungen
3. Steuerungs- und Programmierysteme
3.1. Steuerungen für Schweißroboter
Moderne Robotersteuerungen bieten:
- Integrierte Regelung von Schweißprozess und Roboterbewegung
- Steuerung externer Achsen (Drehtische, Linearführungen)
- Hochwertige Interpolationsalgorithmen für komplexe Bahnen
- Sicherheitsmodule nach ISO/TS 15066
- Schnittstellen zu übergeordneten Produktionssystemen (MES, ERP)
3.2. Schweißstromquellen
Moderne Stromquellen für Roboterschweißen bieten:
- Digitale Prozessregelung im kHz-Bereich
- Fortgeschrittene Betriebsmodi (CMT – Cold Metal Transfer, Pulsbetrieb, AC MIG)
- Echtzeitüberwachung und -protokollierung
- Kommunikationsschnittstellen (EtherNet/IP, Profibus, DeviceNet)
- Adaptive Algorithmen für wechselnde Bedingungen
3.3. Programmiermethoden
Je nach Anforderung kommen verschiedene Programmierverfahren zum Einsatz:
3.3.1. Online-Programmierung
- Teach-In – manuelles Anfahren von Bahnpunkten
- Programmierung über Teach Pendant
- Bewegungserfassung des Bedieners
3.3.2. Offline-Programmierung
- CAD/CAM-Systeme mit Roboterbahnplanung
- Simulationsumgebungen zur Programmvalidierung
- Automatische Bahngenerierung aus CAD-Modellen
- Kollisionsprüfung und Prozessoptimierung
3.3.3. Hybride Systeme
- Offline-Programmierung mit Feinjustage vor Ort
- Parametrische Programme für Variantenvielfalt
- Maschinelles Lernen zur Bahnoptimierung
4. Zubehör und Peripherie
4.1. Drehtische und Positionierer
Diese Komponenten optimieren die Schweißposition und sind entscheidend für die Qualität:
4.1.1. Positionierer-Typen
- Einachsige Drehtische
- Zweiachsige L-Positionierer
- Drei- oder mehrachsige Systeme für volle Orientierungskontrolle
- Mehrstationensysteme mit Werkstückwechsel
4.1.2. Technische Parameter
- Traglasten von wenigen kg bis zu 20 Tonnen
- Wiederholgenauigkeit ±0,1 mm
- Synchronisierung mit Roboterbewegung
- Drehgeschwindigkeiten von 10–120°/s
4.2. Linearführungen und Roboterpositionierung
Für große Arbeitsbereiche werden eingesetzt:
- Bodenmontierte Linearachsen
- Portalsysteme für 3D-Positionierung
- Säulensysteme für hohe Bauteile
- Mobile Roboterlösungen
4.3. Werkstückspannsysteme
Präzises und stabiles Spannen ist entscheidend für die Schweißqualität:
- Spannvorrichtungen mit thermischer Kompensation
- Pneumatische und hydraulische Spannsysteme
- Schnellwechselsysteme
- Integrierte Positioniersysteme
- Sensoren zur Spannungsüberwachung
4.4. Brennerreinigungsstationen
Automatische Reinigungssysteme gewährleisten unterbrechungsfreien Betrieb:
- Mechanische Reinigung der Kontaktdüse
- Entgratung und Spritzerentfernung
- Antihaft-Beschichtungen
- Geometriekontrolle der Brennerspitze
- Automatischer Drahtabschneider
5. Sensorsysteme und Prozessüberwachung
5.1. Nahtverfolgungssensoren
Moderne Systeme nutzen verschiedene Sensoren für adaptive Prozessführung:
5.1.1. Lichtbogensensoren
- Spannungsmessung während Brenneroszillation
- Kantenerkennung durch elektrische Parameteränderungen
- Adaptive Regelung bei variabler Nahtgeometrie
5.1.2. Bildverarbeitungssysteme
- Laserscanner für Geometrieerfassung
- 2D-/3D-Kameras für Echtzeitnahtverfolgung
- Thermografische Überwachung
5.1.3. Tastsensoren
- Werkstückerkennung durch Abtasten
- Geometrievermessung durch Kontakt
5.2. Online-Qualitätskontrolle
Integrierte Echtzeitüberwachungssysteme umfassen:
- Analyse elektrischer Parameter (Spannung, Strom, Lichtbogenstabilität)
- Optische Schweißnahtprüfung
- Ultraschallprüfung für innere Fehler
- Prozessdatenanalyse mit Anomalieerkennung
6. Systemintegration
6.1. Sicherheitseinrichtungen
Roboterschweißzellen erfordern umfassende Sicherheitssysteme:
- Festinstallierte und bewegliche Schutzeinrichtungen
- Lichtschranken und Laserscanner
- Not-Aus-Systeme
- Geschwindigkeitsreduzierung im Programmiermodus
- Normkonformität nach ISO 10218 und ISO/TS 15066
6.2. Absaug- und Filtersysteme
Effektive Rauchabsaugung ist entscheidend für Prozessqualität und Umweltschutz:
- Brennerintegrierte Absaugung
- Zentrale Filtersysteme mit Wärmerückgewinnung
- Luftqualitätsüberwachung
- Materialangepasste Filter
6.3. Integration in Produktionssysteme
Moderne Roboterschweißzellen sind Teil der digitalen Fabrik:
- Anbindung an MES (Manufacturing Execution System)
- Qualitätsmanagementsysteme
- Big-Data-Analysen
- Industrie-4.0-Lösungen mit IoT (Internet of Things)
- Digitale Zwillinge für vorausschauende Wartung
Integriertes Ökosystem
Die Komponenten von Roboterschweißsystemen bilden ein komplexes, integriertes Ökosystem, dessen Effizienz von der richtigen Auswahl und Konfiguration aller Elemente abhängt. Moderne Lösungen zeichnen sich durch Digitalisierung, Adaptivität und Anbindung an übergeordnete Produktionssysteme aus. Schlüsselentwicklungen sind: Autonome Systeme, erweiterte Sensorik, künstliche Intelligenz und ganzheitliche Qualitätskontrolle. Das Verständnis der Komponenten und ihrer Wechselwirkungen ist essenziell für die erfolgreiche Planung, Implementierung und Nutzung von Roboterschweißsystemen in modernen Fertigungsumgebungen.
«zurück